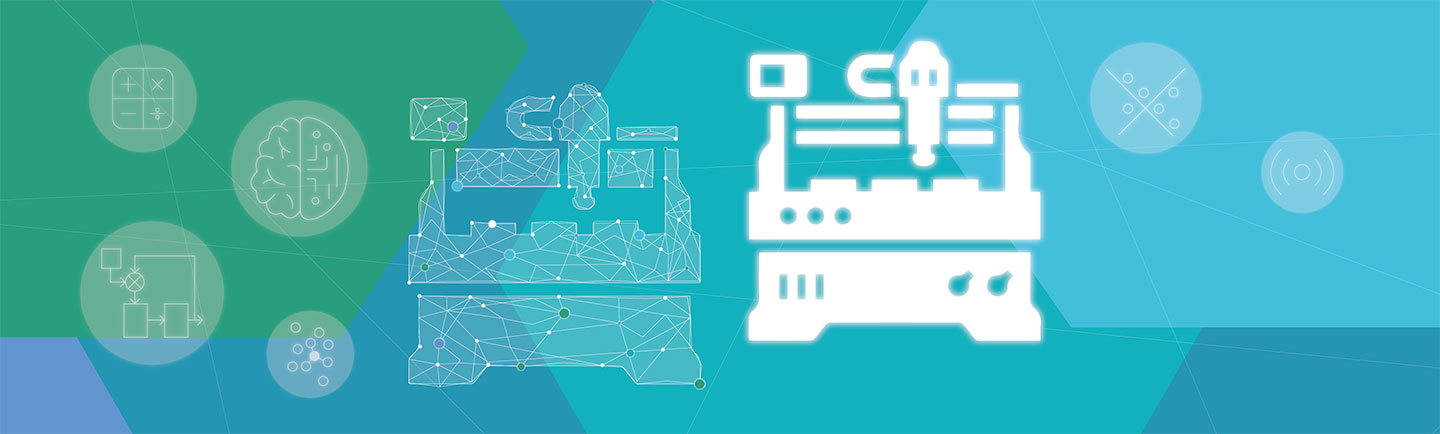
Derzeit reagieren die meisten Industrieunternehmen erst auf auftretende Ausfälle, wenn Maschinen und Anlagen bereits stillstehen (reaktive Instandhaltung), oder führen die Instandhaltung in geplanten Zeitintervallen durch (präventive Instandhaltung). Jedoch führt dies entweder zu kurzfristigen Produktionsausfällen oder teils zu einer Verschwendung von Maschinenarbeitsstunden und Material, weil Komponenten vorzeitig ausgetauscht werden. Die Bestimmung des optimalen Zeitpunkts für die Maschineninstandhaltung zählt nach wie vor zu den großen Herausforderungen in der Produktion. In Krisen verschärfen Engpässe zusätzlich die entstandenen Planungsunsicherheiten.
Mit der Digitalisierung von Produkten und Produktionssystemen kann Ihr Unternehmen diese Problematik vermeiden. Denn ein vielversprechender Lösungsansatz für eine vorausschauende Instandhaltung (Predictive Maintenance) ist das Simulieren derartiger Ausfallszenarien mittels physikbasierter Modellierung und das Anreichern der datengetriebenen Vorhersagemodelle mit den generierten Simulationsdaten. Dies wird mithilfe eines Digitalen Zwillings des Produktionssystems möglich, anhand dessen sich prädiktive Aussagen wie beispielsweise die Restnutzungsdauer (Remaining Useful Life – RUL) von Maschinenkomponenten treffen lassen. Indem Ressourcen und Kapazitäten optimal genutzt werden, spart Ihr Unternehmen nicht nur Kosten, sondern steigert langfristig seine Produktivität und Resilienz.
Wir begleiten Sie umfassend bei der Entwicklung und Anwendung einer auf Ihr Unternehmen zugeschnittenen Industrial Internet-of-Things (IIoT)-Architektur. Dazu greifen wir auf eine Kombination aus bereits etablierten Methoden (z. B. SADT, FMECA oder DoE) sowie auf die Konzeption eines Digitalen Zwillings zurück. Den Grundstein hierfür legt die Hybridisierung datengetriebener und physikbasierter Modelle. Diese Verknüpfung von Engineering und Produktion ermöglicht Ihnen eine erweiterte Datengrundlage zur Vorhersage von Produktionsverläufen, da Sie neben der herkömmlichen Trendextrapolation auf Basis historisch gemessener Daten nun auch bis dato nicht aufgetretene Produktionsausfälle simulieren und verbesserte Vorhersagen treffen können.
Bei der Entwicklung und Umsetzung eines maßgeschneiderten Softwaresystems für Ihr Unternehmen betrachten wir zunächst gemeinsam mit Ihnen die unternehmensspezifischen Anforderungen und Ihre Zielsetzung. Anschließend greifen wir auf ein von uns etabliertes Vorgehen zurück, das aus vier integrativen Phasen besteht:
In Kleingruppenworkshops identifizieren wir die Herausforderungen bei der Einführung eines Digitalen Zwillings in Ihrem Unternehmen und definieren ein Zielbild mit entsprechenden Kennzahlen (z.B. MTBF, OEE). Dazu werden Anwendungsfälle mit unterschiedlichen Anforderungen an den Digitalen Zwilling erarbeitet, um Potenziale bestmöglich auszuschöpfen.
Entlang unserer strukturierten Vorgehensweisen formulieren wir die sogenannte datengetriebene und physikbasierte Modellierung sowie deren Hybridisierung als Grundvoraussetzung für den Digitalen Zwilling. Je nach Reifegrad Ihres Unternehmens in Bezug auf den Digitalen Zwilling variiert der Detailgrad einzelner Teilschritte des erarbeiteten Konzepts.
Wir validieren die Umsetzbarkeit des erarbeiteten Konzepts, indem wir ein Minimal Viable Product (MVP) für Ihren Digitalen Zwilling realisieren. Mithilfe verschiedener Modellierungstechniken und Algorithmen kann bereits ein Teilbereich Ihrer Produkte bzw. Produktionssysteme analysiert und optimiert werden. Um bereits hier mögliche Risiken zu erkennen und zu minimieren, wenden wir ein Proof-of-Concept an.
Wir leiten Handlungsfelder für zukünftige Tätigkeiten in Form von Projektskizzen ab, um eine Grundlage zur Implementierung des für Sie geeigneten Digitalen Zwillings zu schaffen. Hierbei berücksichtigen wir nicht nur die passende Software, sondern auch notwendige Kompetenzen Ihrer Mitarbeitenden sowie organisatorische Aspekte.
Auch nach Projektabschluss begleiten wir Sie gerne weiter, wenn Sie sich Unterstützung bei der Integration des Digitalen Zwillings in allen Unternehmensbereichen wünschen oder Ihre quantitative Key-Performance langfristig bewerten möchten.